Recognizing the Causes and Solutions for Undercut Welding in Metal Manufacture Procedures
In the realm of steel fabrication procedures, the occurrence of undercut welding presents a significant challenge that demands an extensive understanding of its reasons and viable services. The elaborate interaction of numerous variables throughout welding operations can bring about this undesirable phenomenon, influencing the architectural stability and overall quality of the bonded joints - Preventing weld undercut. By dissecting the source of undercut welding and exploring reliable therapeutic steps, fabricators can raise the standard of their craftsmanship and guarantee the manufacturing of remarkable steel parts
Common Root Causes Of Undercut Welding
Often forgotten in metal fabrication, undercut welding takes place due to different factors that require meticulous focus and competence to be efficiently minimized. One common reason for undercut welding is too much heat input. When the warm input is too expensive, it can bring about the melting and subsequent erosion of the base material along the sides of the weld joint, creating a groove or undercut. In addition, improper welding techniques, such as utilizing the incorrect welding angle or take a trip rate, can also contribute to undercut formation. Poor protecting gas insurance coverage is one more key factor that can cause damaging. Inadequate gas protection stops working to shield the weld swimming pool sufficiently, resulting in oxidation and undercut issues. The option of welding criteria, such as voltage, current, and cable feed rate, plays a significant duty in the occurrence of undercut welding. Recognizing these usual reasons is essential for applying preventive measures and guaranteeing premium welds in metal manufacture processes.
Effect of Incorrect Welding Parameters
Unreliable welding criteria can considerably endanger the honesty and quality of welded joints in steel manufacture procedures. The impact of inaccurate welding specifications shows up in numerous ways, leading to structural weaknesses and flaws in the bonded parts. Meticulous interest to welding specifications is extremely important to ensure the production of top quality welds with the preferred mechanical residential properties and architectural honesty.
Result of Improper Torch Angle
Improper torch angle in welding procedures can substantially affect the high quality and integrity of the final weld joints in steel construction processes. Undercutting is an usual welding flaw where a groove develops along the weld toe, compromising the joint and compromising its architectural stability.
A torch angle that is too high can cause inadequate penetration, insufficient blend, and boosted spatter. On the other hand, a torch angle that is also shallow can result in too much infiltration, burn-through, and distortion of the base material. Preventing weld undercut. Correct lantern angle is vital for guaranteeing consistent weld top quality, stamina, and appearance
To avoid damaging and various other problems caused by inappropriate torch angles, welders must be educated to maintain the proper torch angle throughout the welding procedure. Routine monitoring and modification of torch angles throughout welding can help attain sound welds with marginal problems.
Duty of Inadequate Welding Methods
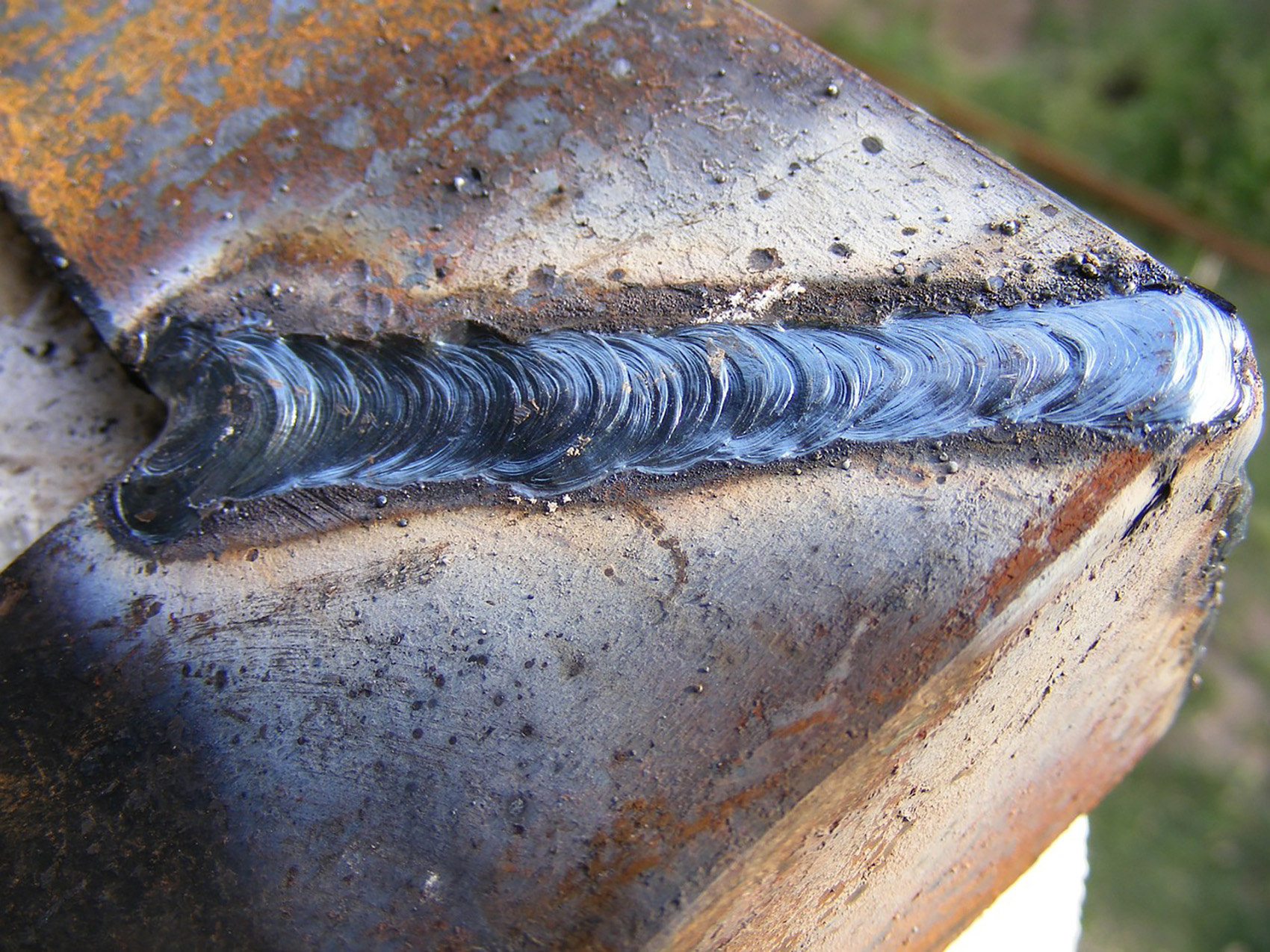
Another aspect of inadequate welding techniques is improper weld prep work. Poor cleansing of the base steels, inaccurate joint design, or insufficient edge prep work can all add to damage welding. Insufficient shielding gas insurance coverage or making use of the incorrect type of gas can result in visite site insufficient blend and the formation of undercut defects.
To resolve the duty of insufficient welding techniques in steel construction processes, it is vital to give thorough training for welders. Appropriate education on welding criteria, joint preparation, and shielding gas option can assist prevent undercut welding and make certain top notch welds in metal manufacture jobs.
Effective Solutions for Undercut Welding
Addressing undercut welding in steel fabrication calls for applying reliable options to enhance weld high quality and structural stability. One of the main solutions to battle undercut is to adjust welding criteria such as voltage, current, and take a trip rate to guarantee correct heat input and blend. By fine-tuning these Source settings, welders can stop too much melting of the base metal and filler product, reducing the probability of undercut formation.
Furthermore, correct joint preparation is vital in preventing undercut. Making sure tidy base metal surfaces complimentary of contaminants and utilizing the proper bevel angle can help promote much better weld infiltration and reduce the danger of undercut - Preventing weld undercut. Utilizing ideal welding techniques, such as weaving or oscillating the torch, can additionally aid in distributing heat uniformly and filling up the weld joint appropriately, minimizing the possibility of undercut flaws
In addition, picking the correct welding consumables, including electrodes and filler metals, is necessary in minimizing undercut. Making use of materials with appropriate chemical compositions and mechanical buildings can add to achieving audio welds with minimal undercut. Regular inspection and quality assurance steps ought to likewise be executed to discover and deal with undercut problems immediately, making sure this post the general stability of fabricated metal parts.

Conclusion
Finally, understanding the reasons and remedies for undercut welding in steel construction processes is essential for achieving top quality welds. By addressing usual reasons such as inaccurate welding parameters, improper lantern angle, and insufficient welding techniques, welders can prevent damaging and make sure strong, durable welds. It is vital to pay focus to these aspects and execute reliable options to enhance the overall welding procedure and final item high quality.
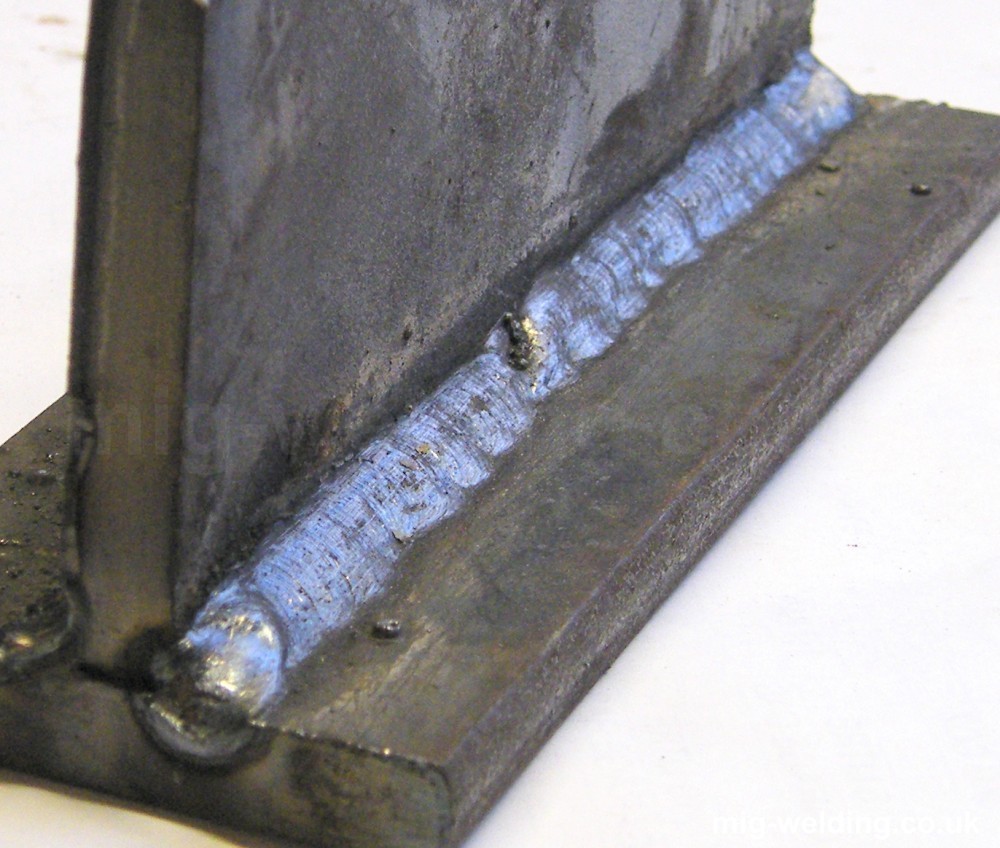